HEC und Andyson: Einblicke in die Fertigung von Netzteilen in China
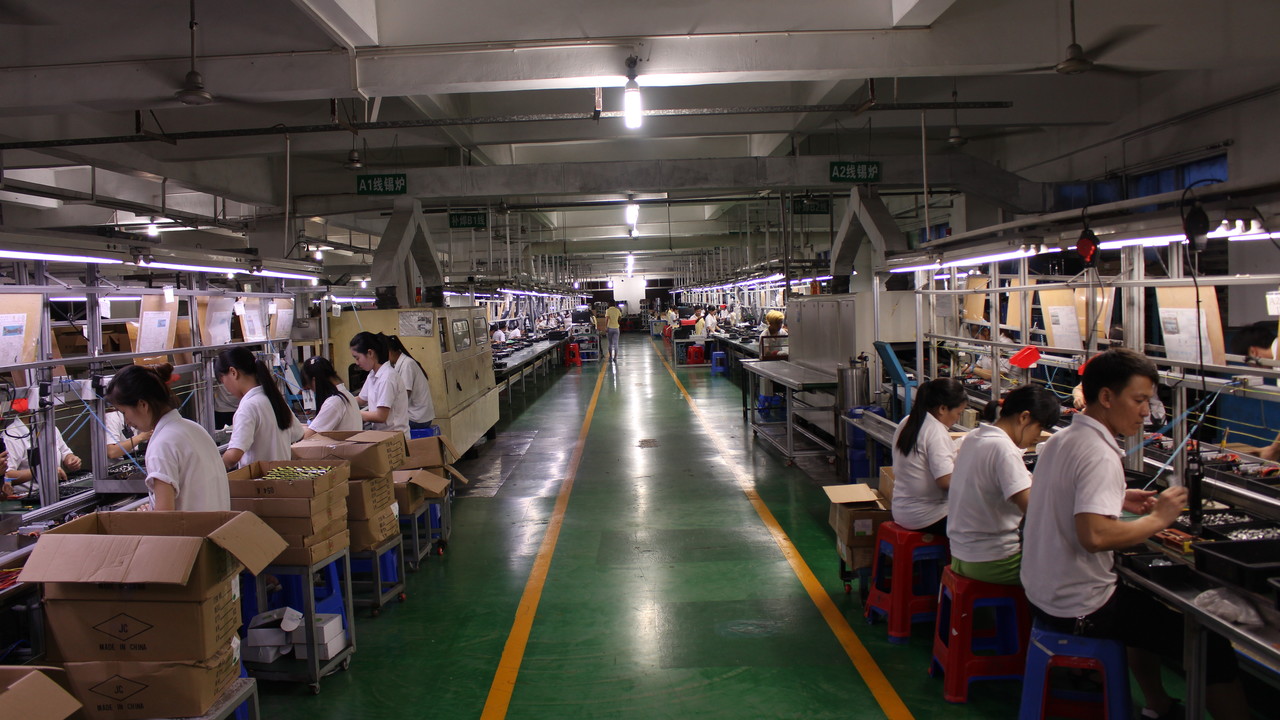
tl;dr: ComputerBase hat auf Einladung von Aerocool im Rahmen der Computex 2017 Einblicke in den Produktionsprozess von Netzteilen bei HEC und Andyson gewinnen können. An den chinesischen Standorten in Shenzhen und Dongguan lässt sich einiges über die Fertigung von Netzteilen erfahren, auch warum sie so günstig sind.
Hohe Wertschöpfungstiefe bei HEC
Die Produktionsstätte von HEC befindet sich derzeit noch in einem aufstrebenden Bezirk von Shenzhen, den das Unternehmen in diesem Jahr aber noch verlassen möchte. Am aktuellen Standort zählt das vor über 30 Jahre errichtete Gebäude zu den älteren Bauwerken, dem das subtropische Klima schon stark zugesetzt hat. Mit 2.000 Mitarbeitern auf 2,5 Hektar gehört das Werk zu einem der größeren in der Branche, das Werk von Andyson fällt deutlich kleiner aus. Die derzeitigen Kapazitäten umfassen maximal vier Produktionslinien und drei SMD-Montage-Linien. Am neuen Standort sollen die Kapazitäten weiter ausgebaut werden.
Im Werk von HEC werden sehr viele Schritte der Wertschöpfungskette selbst durchgeführt. Von der Gehäusefertigung über die SMD-Bestückung der Platinen bis hin zur Qualitätskontrolle und Endmontage findet der überwiegende Teil des Produktionsprozesses in der Fabrik statt.
Komponenten-Vorbereitung
Eine vorbereitende Maßnahme für die Produktionslinie besteht in der Veredelung der Bauelemente. Damit die Komponenten mit Durchsteckmontage am Fließband ohne zusätzlichen Aufwand eingesetzt werden können, müssen Beinchen abgeschnitten sowie teilweise gebogen und isoliert werden. Dieser Prozess verläuft mit Maschinen teilautomatisiert – insbesondere für das Biegen der MOSFET-Beinchen ist ein maschinelles Verfahren entscheidend, um Defekte durch eine fehlerhafte mechanische Verformung ausschließen zu können. Die Maschinen sind alt und abgeschrieben, verrichten aber noch zuverlässig ihren Dienst.
Nur die Montage der Halbleiterbauelemente auf einem Kühlkörper geschieht per Hand. Der Kühlkörper samt Leistungshalbleiter wird anschließend als Ganzes an die Produktionslinie übergeben.
Verarbeitung und Bestückung der Platinen
Die Platinen erreichen das Werk unbestückt, aber bis auf die Bohrlöcher komplett verarbeitet. Im ersten Schritt werden die Bohrlöcher im Falle von Pertinax-Platinen mit einzelner Leiterbahn vollautomatisch ausgestanzt. Anschließend werden die SMD-Komponenten montiert. Dazu wird zunächst Kleber an die Stellen der Platine aufgetragen, auf welche die Bauteile gesetzt werden sollen. Vollautomatische Bestückungsautomaten sowohl für DC-DC-Tochterplatinen als auch für die Hauptplatinen von Netzteilen platzieren nun SMD-Bauteile an die entsprechenden Stellen. Nach diesem Schritt werden die Bauteile schließlich in einem Ofen im Wiederaufschmelzlötverfahren auf die Platine gelötet. Mitarbeiter müssen sich um den Austausch leerer Rollen für die Bestückungsautomaten kümmern, davon abgesehen wurde der Fertigungsprozess jedoch größtenteils automatisiert.
Anschließend erfolgt eine Bestückung mit kleinen radialen Bauelementen, die ebenfalls automatisch in die Platine eingesetzt werden können. Die Bauelemente – überwiegend Elkos und Transistoren – werden dabei über einen Gurt zugeführt, so wie sie von den Zulieferern übergeben werden.
Bauelemente-Bestückung auf der Produktionslinie
Ein großes Aufgabengebiet der manuellen Produktionslinie besteht im Einsetzen großer bedrahteter Bauelemente. Jeder Mitarbeiter ist dabei für die Bestückung weniger Komponenten zuständig. Die Technologie des Netzteils entscheidet dabei über den Aufwand für die Produktionslinie, der mit teureren Technologien weiter zunimmt. In einer 10-Stunden-Schicht können demnach auf zwei Produktionslinien entweder 1.700 Netzteile einfacherer Technik (Double Forward mit Gruppenregulierung) oder 1.200 Netzteile komplexerer Technik (LLC-Resonanzwandler mit DC-DC-Wandlern) hergestellt werden; die Kosten der Fertigung liegen also um gut ein Drittel höher.
Spulen und Transformatoren werden in einem zweiten Werk von HEC gewickelt; nur die Kabel werden von anderen Herstellern zugeliefert. Nachdem alle Komponenten platziert wurden, wird eine Halterung auf die Komponenten gesetzt, die eine maßgeschneiderte Form für das jeweilige Netzteil besitzt. Eine Arretierung der Bauteile ist notwendig, damit diese beim Lötvorgang richtig ausgerichtet sind und sich nicht mehr bewegen. In der Wellenlötanlage wird die Unterseite der Platine für eine möglichst kurze Zeit über eine Lotwelle gezogen, um die Bauteile nicht thermisch zu beschädigen. Diese Zeitspanne kann durch Vorheizen des kompletten Netzteils verkürzt werden, weshalb vor dem eigentlichen Lötvorgang das Netzteil bereits in einem Ofen auf Temperatur gebracht wird.
Funktionstests und Endmontage (HEC)
Nach dem Lötvorgang werden die Lötstellen mit optischen Verfahren überprüft. Mitarbeiter markieren die fehlerhaften, meist unbenetzten Lötstellen, die im nächsten Schritt von Hand nachgebessert werden. Anschließend wird das Netzteil erstmals einem Funktionstest unterzogen. Besteht es diesen nicht, wird das Netzteil an die vorherige Station übergeben, an der der Fehler behoben werden soll.
Im nächsten Schritt erfolgt der Zusammenbau des Netzteils, der mit dem Vorbereiten des Gehäuses beginnt. Dieser schließt den Einbau der Kaltgerätebuchse, des Netzschalters und des Erdungskabels ein und erstreckt sich anschließend über das Zusammenlöten dieser Komponenten gemeinsam mit den Netzfilter-Elementen an der Kaltgerätebuchse. Mit Kabelbindern werden schließlich die Kabel mit dem Gehäuse fixiert und mit Kleber werden große Bauteile im Netzteil befestigt, um Lötstellen mechanisch zu entlasten.
Nachdem das Netzteil zusammengeschraubt wurde, folgen weitere Funktionstests. Darin inbegriffen sind eine Hochspannungsprüfung „Hipot“, bei der die elektrische Isolation getestet wird, ein Test aller Anschlüsse und ein Chroma-Lasttest zur Überprüfung der elektrischen Performance. Zur Verringerung der Ausfallquote wird ein „Burn In“-Lasttest durchgeführt. Die Ausfallverteilung über der Zeit gleicht nämlich einer Badewannenkurve, weshalb in diesem Schritt ein Großteil der defekten Netzteile aussortiert werden kann: Was nicht hält, fällt in der Regel gleich durch. Jedes Netzteil wird dafür für 40 Minuten mit 80 Prozent der Nennleistung ausgelastet. Um das Netzteil einer noch stärkeren Belastung auszusetzen, wird außerdem die Netzspannung immer wieder unterbrochen. Fällt ein Netzteil in einem dieser Tests durch, wird versucht eine Reparatur durchzuführen.
Andyson lässt Platinen und Gehäuse zuliefern
Die Fabrik von Andyson in Dongguan ist gegenüber der von HEC überschaubar: Über zwei Stockwerke gibt es nur zwei statt vier Produktionslinien und keine SMD-Bestückung. Wie die bestückten Platinen werden auch die Gehäuse extern zugeliefert. Die Wertschöpfungskette ist entsprechend geringer.
Produktionslinien unterschiedlicher Ausstattung
Die Komponenten-Vorbereitung wie das Anschrauben der Halbleiterbauelemente auf den Kühlkörper erfolgt parallel auf der Produktionslinie. Auf dieser werden von Andyson selbst auch noch die großen bedrahteten Komponenten und zum Schluss die Kabel der DC-Ausgangsschienen eingesetzt. Auch hier gibt es für jedes Netzteilmodell eine maßgeschneiderte Halterung zur Fixierung der Bauteile für das Wellenlöten.
Mit der Wellenlötanlage fällt ein erster Unterschied zwischen den beiden Produktionslinien auf, die auf der einen Linie ein neueres Modell als auf der anderen ist. Anschließend erfolgt eine manuelle Inspektion ohne die Hilfe einer Bildverarbeitung. Einzig die Detektion überstehender Pins wurde mittels einer Maschine automatisiert, die dafür eine Lichtschranke einsetzt.
Funktionstests und Endmontage (Andyson)
Die nachfolgenden Schritte unterscheiden sich wiederum kaum von denen bei HEC. So werden vor der Gehäusemontage erste Tests durchgeführt und gegebenenfalls Lötverbindungen zur Nachbesserung reklamiert. Für das Zusammenschrauben kann nach Wunsch des Auftraggebers eine Schablone eingesetzt werden, mit der das Verkratzen des Gehäuses und Hineinfallen einer Schraube in das Netzteil vermieden werden können. Für eine tiefergreifende Reparatur eines Netzteils gibt es am Ende der Produktionslinie Arbeitsplätze, die komplett mit Laborgeräten ausgerüstet sind, um beispielsweise fehlerhafte Komponenten zu erkennen und auszutauschen.
Für den „Burn In“-Test hat Andyson einen Wärmeschrank eingerichtet, der die Umgebungstemperatur für die Netzteile auf 40 °C konstant hält. Außerdem erstreckt sich ein Test über eine ganze Stunde anstatt 40 Minuten. Für jedes Modul kann eine Last von bis zu 500 Watt eingestellt werden, weshalb für Netzteile mit einer Ausgangsleistung von mehr als 625 Watt zwei Module benötigt werden, um eine 80-prozentige Auslastung erzielen zu können.
Abschließende Tests mit Qualitätskontrolle
Als Teil der Qualitätskontrolle wird aus jeder Charge eine bestimmte Anzahl an Netzteilen entnommen, die zusätzliche Tests durchlaufen müssen. Dabei werden unter anderem Testsysteme eingesetzt, um das Netzteil auf dynamische Belastungen hin zu testen.
Vor dem Verpacken werden abschließende Lasttests durchgeführt. Hochspannungs-, Last- und Rütteltests werden dabei auf einem Arbeitsplatz gemeinsam vollzogen. Darauffolgend wird ein umfangreicherer Lasttest an einer Chroma-Teststation veranlasst, wobei sich hier die beiden Produktionslinien bezüglich der Ausstattung unterscheiden, weil die eine Linie mit einer Chroma 8000 anstatt 6000 ausgerüstet ist. Für den elektrischen Test der Stecker verwendet Andyson ebenso ein Messintrument, das die Kontaktierung aller Pins prüft. Im letzten Schritt wird das Netzteil schließlich in die Einzelhandelsverpackung abgepackt.
Fazit
HEC genießt mit der zentralen Gehäusefertigung ein Alleinstellungsmerkmal in der Branche. Die Netzteilgehäuse sind dabei aber nur ein Nebenprodukt, weil auch PC- und Server-Gehäuse in dieser Fabrik vom Band laufen. Für andere Hersteller bedeutet die Zulieferung der Gehäuse zusätzliche Kosten im Einkauf. Ungeachtet der längeren Wertschöpfungskette bei HEC gibt es wiederum große Ähnlichkeiten der Produktionslinien von Andyson und HEC. Neben dem Ablauf der Produktionsschritte sind auch Überschneidungen in den sonderangefertigten Messgeräten wie dem Stecker-Prüfgerät erkennbar.

Neue Welt – alte Welt
In der Leistungselektronik gibt es den Trend hin zu immer kompakteren Bauformen, die beispielsweise durch den Einsatz von SMD-Komponenten auf möglichst allen Ebenen begünstigt werden. Mit der Vorherrschaft des ATX-Formats liegt die Innovationskraft dahingehend aber noch brach – und auch der Kostendruck und die Unwissenheit der Kunden hemmt den Fortschritt in diesem Segment. Ein weiteres Resultat ist, dass die in China besichtigten Produktionslinien zwar die Ansprüche an den erforderlichen Produktionsprozess erfüllen, Innovation aber gänzlich vermissen lassen. Viele ältere Anlagen spiegeln den hohen Kostendruck der Branche, in der Netzteile für um die 50 Euro Kassenschlager sind, wider. Das zeigt sich auch an den verwendeten Prüf- und Messgeräten, die zwar ihren Zweck erfüllen, aber nicht durchgehend auf dem aktuellen Stand der Technik sind.
Fließbandarbeit kein Zuckerschlecken
Die Netzteilherstellung findet fast ausschließlich in China statt, da vergleichsweise geringe Lohnkosten und kürzere Transportwege zur Beschaffung aller Bauteile ein Vorteil für diesen Standort sind. Die geringen Verkaufspreise hinterlassen aber auch ihre Spuren bei den Arbeitsbedingungen. So müssen lange Schichten bei zum Teil unergonomischer Körperhaltung unter Umgebungstemperaturen von rund 30 °C bei hoher Luftfeuchtigkeit durchgehalten werden. Als einzige Ausnahme sticht der klimatisierte Raum für die SMD-Bestückung bei HEC hervor. Genauso wie die Arbeitsbedingungen nimmt auch die Arbeitssicherheit einen anderen Stellenwert in China ein, sie kann nicht mit der aus Deutschland bekannten verglichen werden.
ComputerBase konnte die beiden Auftragsfertiger im Rahmen der Computex 2017 auf Einladung von Aerocool besichtigen. Der Hersteller gibt Netzteile bei beiden Unternehmen in Auftrag. Die Kosten für Anreise und Unterkunft wurden vom Hersteller getragen, die Kosten für das Visum von ComputerBase.
Dieser Artikel war interessant, hilfreich oder beides? Die Redaktion freut sich über jede Unterstützung durch ComputerBase Pro und deaktivierte Werbeblocker. Mehr zum Thema Anzeigen auf ComputerBase.