Vom Silizium zum Die: So werden aus Wafern im Reinraum Chips
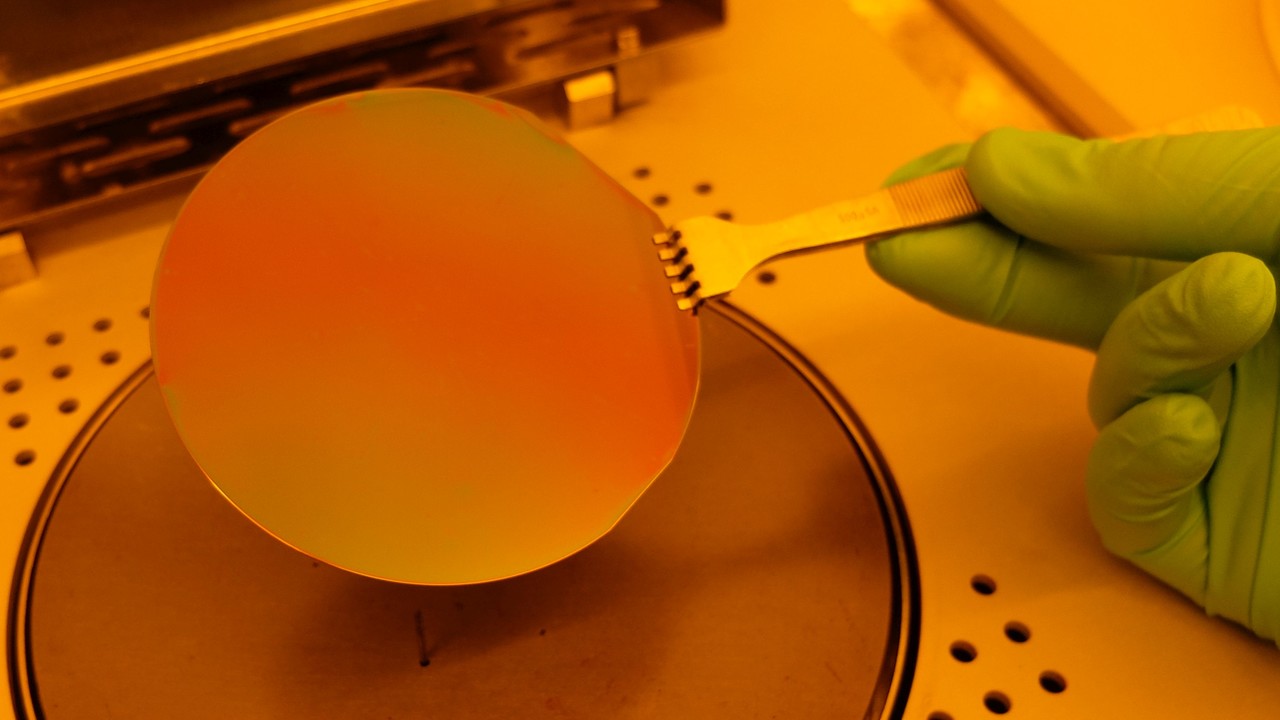
tl;dr: Das tägliche Leben wird von Silizium beherrscht: Vom PC über das Auto bis zum Smartphone und Kühlschrank, überall finden sich heutzutage Mikrochips. Dazu werden Wafer im Reinraum prozessiert. Doch wie funktioniert das? ComputerBase konnte die Fertigung von Mikroheizelementen auf Silizium-Wafern verfolgen.
Silizium-Wafer setzen einen Reinraum voraus
Am Institut für Mikrosystemtechnik (IMTEK) der Universität Freiburg hat ComputerBase die Prozessierung von Wafern im Reinraum begleitet. Auf den Siliziumscheiben entstehen dabei zwar keine Transistoren, wie sie für Prozessoren benötigt werden. Doch die simpleren Heizelemente, die hergestellt wurden, bieten einen guten Einstieg in die Vorgänge im Reinraum. Dieser Bericht hat nicht den Anspruch eines wissenschaftlichen Artikels, sondern soll dem interessierten Leser lediglich einen kleinen Einblick in die Welt der Mikrosysteme bieten.
Silizium ist ein häufiges Element, das nicht nur als Grundlage von Transistoren eine große Rolle spielt: Sand besteht zum großen Teil aus dem Element, und im Alltag des Menschen ist es beispielsweise in Form von Glas seit langer Zeit quasi unverzichtbar. Als Scheiben aus hochreinem Silizium (sogenannten Wafern) findet es Verwendung in der Mikroelektronik und Mikrosystemtechnik.
Gegen Verunreinigungen: Der Reinraum
Um überhaupt sinnvoll mit dem Halbleiter arbeiten zu können, ist ein gewaltiger Aufwand notwendig. Denn um Strukturen in der Größenordnung von Mikro- oder sogar Nanometern auf das Silizium aufzubringen, dürfen keine Verunreinigungen auf die Wafer gelangen. Als Größenvergleich: Ein menschliches Haar hat einen Durchmesser von etwa 100 µm (0,0001 m); in der Industrie wird mit Strukturgrößen bis hinunter in den zweistelligen Nanometerbereich gearbeitet – also ein Zehntausendstel der Dicke eines Haares oder auch 0,00000001 m. Hautschuppen, Haare und andere Partikel, die in unserer Umgebung durch die Luft schwirren, wären für die Herstellung dieser Produkte fatal. Ein einziger Fehler bei der Generierung der Strukturen kann das Produkt am Ende der Arbeitskette zerstören, weshalb für ein passendes Umfeld gesorgt werden muss, das rein genug für die Prozessierung der Wafer ist: Ein Reinraum wird vorausgesetzt.
Das ist bereits ein Schritt, um für eine hohe Ausbeute (Yield-Rate) der hergestellten Produkte zu sorgen. Hohe Yield-Raten setzen selbstverständlich auch präzises Equipment und erprobte und standardisierte Produktionsverfahren voraus. Für den Betrieb eines Reinraums sind hohe laufende Kosten zu tragen, denn neben einer konstanten Luftumwälzung inklusive Filterung gegen besagte Partikel müssen auch die Temperatur sowie Luftfeuchtigkeit konstant gehalten werden.
Reinräume werden in verschiedene Kategorien eingeteilt, welche sich auf die erlaubte Anzahl und Größe für Partikel in der Luft beziehen. Dabei ergeben sich auch Unterschiede bezüglich der notwendigen Reinraumkleidung, denn um Verunreinigungen vorzubeugen, werden für das dort arbeitende Personal wenigstens Reinraumanzüge, Überschuhe, Handschuhe und Haarnetze vorausgesetzt. In Bereichen, wo mit gefährlichen Substanzen wie etwa der ätzenden Flusssäure (HF) gearbeitet wird, werden weitere Schutzmaßnahmen benötigt. Besonders sensible Prozesse setzen zusätzliche Ausrüstung voraus und werden weitestgehend automatisiert, um den Menschen als Kontaminationsquelle auszuschließen.
Kontrolliertes Einschleusen
Ebenso wie Personen Verunreinigungen in die kontrollierte Umgebung transportieren könnten, gilt dies auch für Arbeitsmaterial. Daher werden sämtliche Geräte und Materialien gründlich gereinigt, bevor sie die Schleuse in den Reinraum passieren dürfen. Aus diesem Grund durften Bilder auch ausschließlich mit der Reinraumkamera, die vor Ort im Reinraum zur Verfügung steht, aufgenommen werden. Auch Silizium-Wafer werden nach der Ankunft im Reinraum zunächst gereinigt, bevor die Arbeit beginnt. Mit aggressiver Caroscher Säure werden eventuell vorhandene organische Reste auf der Silizium-Oberfläche entfernt.
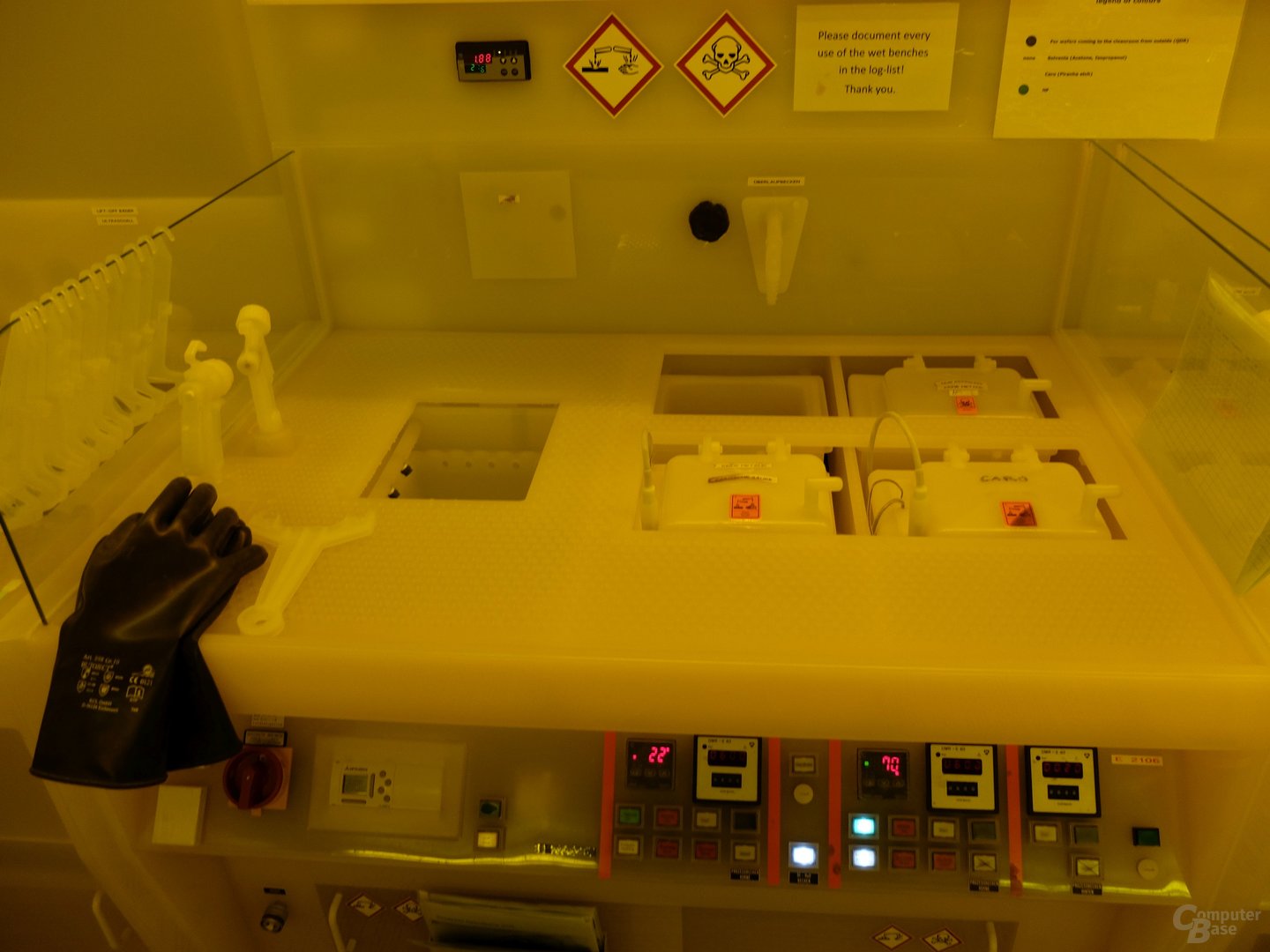
Einige Aufnahmen zeigen ein scheinbares Versagen des automatischen Weißabgleichs der Kamera: Bilder mit Gelbstich stammen aus Bereichen, in welchen mit lichtsensitivem Lack gearbeitet wird. Für die Fotolithographie werden Wafer mit noch unbelichtetem Fotolack beschichtet. Räume mit gelbem Licht entsprechen daher den Dunkelkammern alter Fotolabors, allerdings mit dem Unterschied der kritischen Wellenlängen: Im Gegensatz zum Film von Fotoapparaten, der langwelligem rotem Licht ausgesetzt werden kann, ohne belichtet zu werden, sind die Fotolacke der Lithographie im UV-Bereich sensitiv, weshalb Licht im gelben Bereich des sichtbaren Spektrums noch keine Gefahr darstellt. Erst die kurzwelligeren Anteile im blauen und ultravioletten Bereich könnten für eine ungewollte Belichtung sorgen.
Die Schritte bis zur Belichtung
Nachdem die 4"-Wafer (100 Millimeter Durchmesser, bei Mikrochips sind 300 mm State-of-the-Art) gereinigt wurden, wird die Oberfläche behandelt, um den Halbleiter mit einer Oxid- und Nitridschicht auszustatten. Zunächst wird eine Oxidschicht erzeugt, indem die Wafer bei etwa 1.000 °C von Wasserdampf überströmt werden. Dadurch wächst eine Siliziumdioxid-Schicht in die Wafer ein. Auf diese thermische Oxidation folgt die Ablagerung von Siliziumnitrid. Dies wird über eine chemische Gasphasenabscheidung (CVD) erreicht, bei der aus Monosilan und Ammoniak bei Temperaturen jenseits von 500 °C eine chemische Reaktion auf der Wafer-Oberfläche ausgelöst wird, so dass Siliziumnitrid abgeschieden wird. Diese Schichten dienen unter anderem der elektrischen Isolation, denn später werden dünne Metalllinien auf den Wafern abgelagert, welche als Heizelement dienen, sobald sie von elektrischem Strom durchflossen werden.

Der nun vorbereitete Wafer ist absolut blank und spiegelnd. Bevor Strukturen aufgetragen werden können, muss zunächst ein Fotolack (englisch „Resist“) auf dem Wafer verteilt werden. Diese Lacke werden in die zwei großen Gruppen der Positiv- und Negativlacke unterteilt. Beiden Varianten ist gemein, dass eine lichtsensitive Komponente („photoactive compound“) enthalten ist, die durch Belichtung mit UV-Licht ihre Eigenschaften ändert.
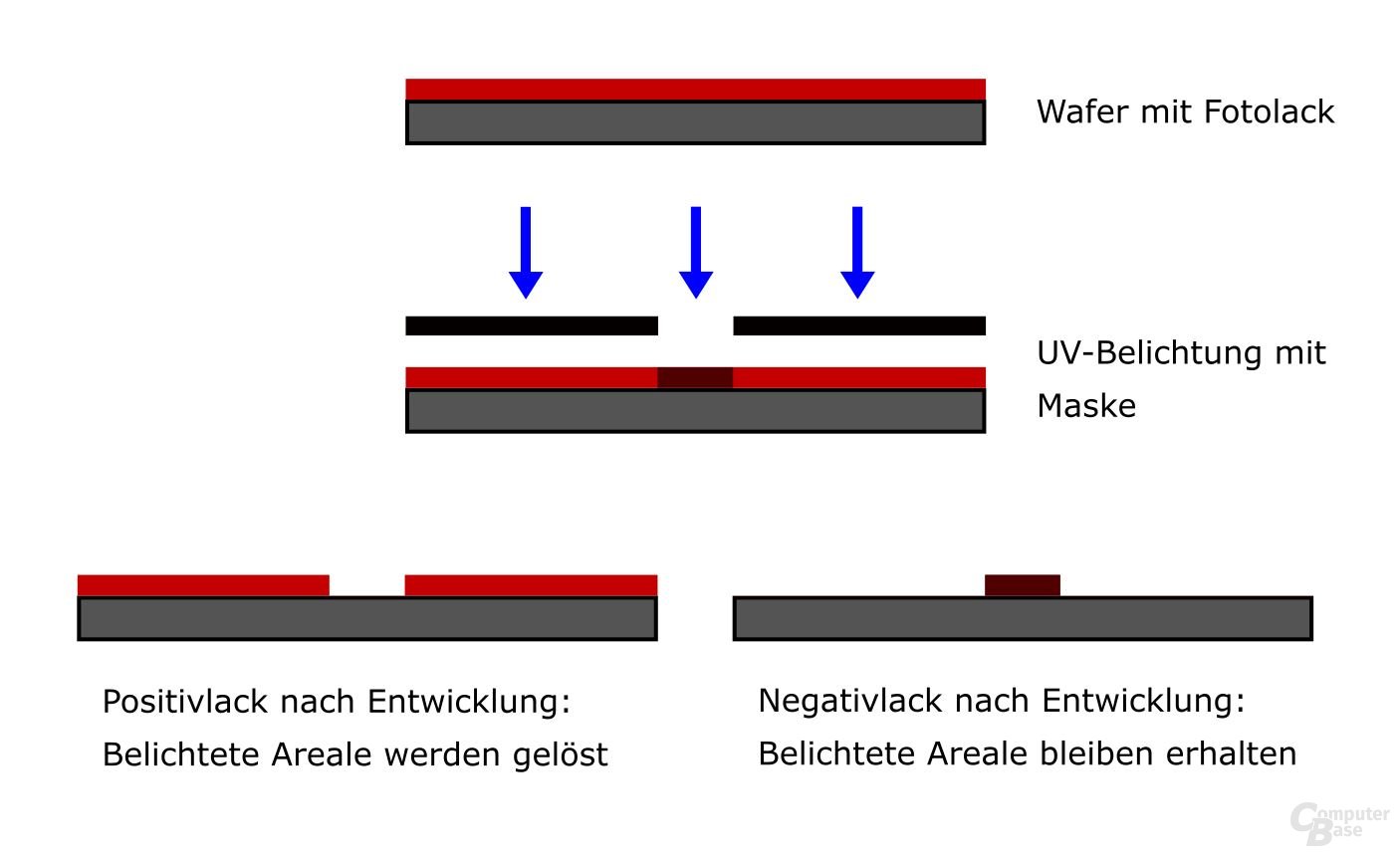
Positivlack wird bei Belichtung löslicher, während Negativlack in belichteten Arealen an Löslichkeit verliert. Nach der Belichtung mit einer eigens angefertigten Maske werden die Lacke entwickelt – dabei werden nur die löslichen Bereiche entfernt, so dass beim Positivlack die belichteten Bereiche abgewaschen werden, wohingegen diese beim Negativlack erhalten bleiben.
Der Lack wird per Rotationsbeschichtung („spin-coating“) aufgetragen: Die Wafer werden über ein Vakuum auf einem Teller angesaugt, der mit einer bestimmten Drehzahl rotiert. Abhängig vom Fotolack sowie der Umdrehungsgeschwindigkeit wird dadurch eine definierte Schichtdicke erreicht. Im Anschluss werden durch einen Heizschritt unerwünschte Lösungsmittel aus der Lackschicht entfernt, welche unter anderem zur Verunreinigung der Maske bei der nachfolgenden Belichtung führen könnten.
Mit Maske und dem richtigen UV-Licht
Zur Belichtung wird nicht nur eine UV-Lichtquelle, sondern auch die Maske vorausgesetzt. Die Maske enthält das negative oder positive Abbild der gewünschten Strukturen – abhängig davon, ob ein Positiv- oder Negativ-Lack genutzt wird und welche Schritte im Anschluss durchgeführt werden. Der Belichtungsprozess selbst findet mit einem „Mask Aligner“ statt, mit welchem zunächst dafür gesorgt wird, dass Belichtungsmaske und Wafer richtig zueinander ausgerichtet sind. Das ist zwingend erforderlich: Abhängig von der Komplexität des Produktes werden im Laufe der Prozessierung mehrere Masken benötigt, die je eine bestimmte Struktur tragen, welche in einem folgenden Schritt über verschiedene Prozesse irreversibel auf den Wafer übertragen werden können. Über den Fotolack werden diese zunächst per UV-Licht als Vorlage auf die Wafer gebracht.
In diesem Fall besteht die verwendete Maske aus Quarzglas, welches die Strukturen der Heizelemente in Form einer Chromschicht trägt. Diese Maske wird in geringem Abstand (etwa 50 µm) über dem Wafer ausgerichtet und anschließend von oben über eine Quecksilberdampflampe beleuchtet. Für die Heizelemente reicht eine Strukturgröße im Mikrometer-Bereich, weshalb die Belichtung mit diesem Abstand möglich ist. Niedrigere Abstände erhöhen die Auflösung – aber auch das Risiko, die Maske durch den Kontakt mit dem Wafer zu beschädigen. Die kleinste Strukturgröße der Heizelemente liegt bei 24 µm.
Masken können teuer sein
Die Quarzglas-Maske ist mit unter 1.000 Euro noch günstig, denn in der Industrie können hochauflösende Masken durchaus auch im Millionenbereich landen. Um den Verschleiß der teuren Masken zu verringern und möglichst hohe Auflösungen zu erreichen, werden dort optische Verfahren eingesetzt, mit welchen die Masken über Linsensysteme auf die Wafer projiziert werden. Zudem muss Licht mit zunehmend kleineren Wellenlängen für die Belichtung eingesetzt werden, denn bei optischen Systemen limitiert die eingesetzte Wellenlänge die erreichbare Auflösung: Je kleiner die Wellenlänge, desto höher die erreichbare Auflösung.
Neben der korrekten Ausrichtung von Wafer und Maske bei aufeinanderfolgenden Belichtungsprozessen muss beim Wafer zudem auf die richtige Orientierung geachtet werden. Die Wafer sind zwar als runde Scheiben ausgelegt, besitzen jedoch eine abgeflachte Seite, das sogenannte „Flat“. Dieses dient nicht nur als Orientierungshilfe, sondern gibt auch die Ausrichtung des Silizium-Kristallgitters an – das ist für manche Prozesse wie anisotropes Ätzen (richtungsabhängiges Ätzen in das Silizium, zum Beispiel per Kaliumhydroxid) relevant, die sich nicht in alle Richtungen des Kristallgitters gleichermaßen ausbreiten.
Beim Alignment der ersten Maske wird das Flat des Wafers zu vorgegebenen Strukturen auf der Maske ausgerichtet. Um das Alignment für folgende Masken zu erleichtern, werden mit der Maske zudem Orientierungspunkte auf den Wafer übertragen, die als Ausgangspunkt für weitere Masken dienen. Im Anschluss erfolgt die Belichtung, wobei hier die i-Linie, h-Linie und g-Linie des Spektrums der Quecksilberdampflampe genutzt werden. Kurzwelligere UV-Strahlung oder eine feinere Auswahl des Lichtspektrums über einen Filter ist bei der benötigten Auflösung für die Heizelemente nicht notwendig.
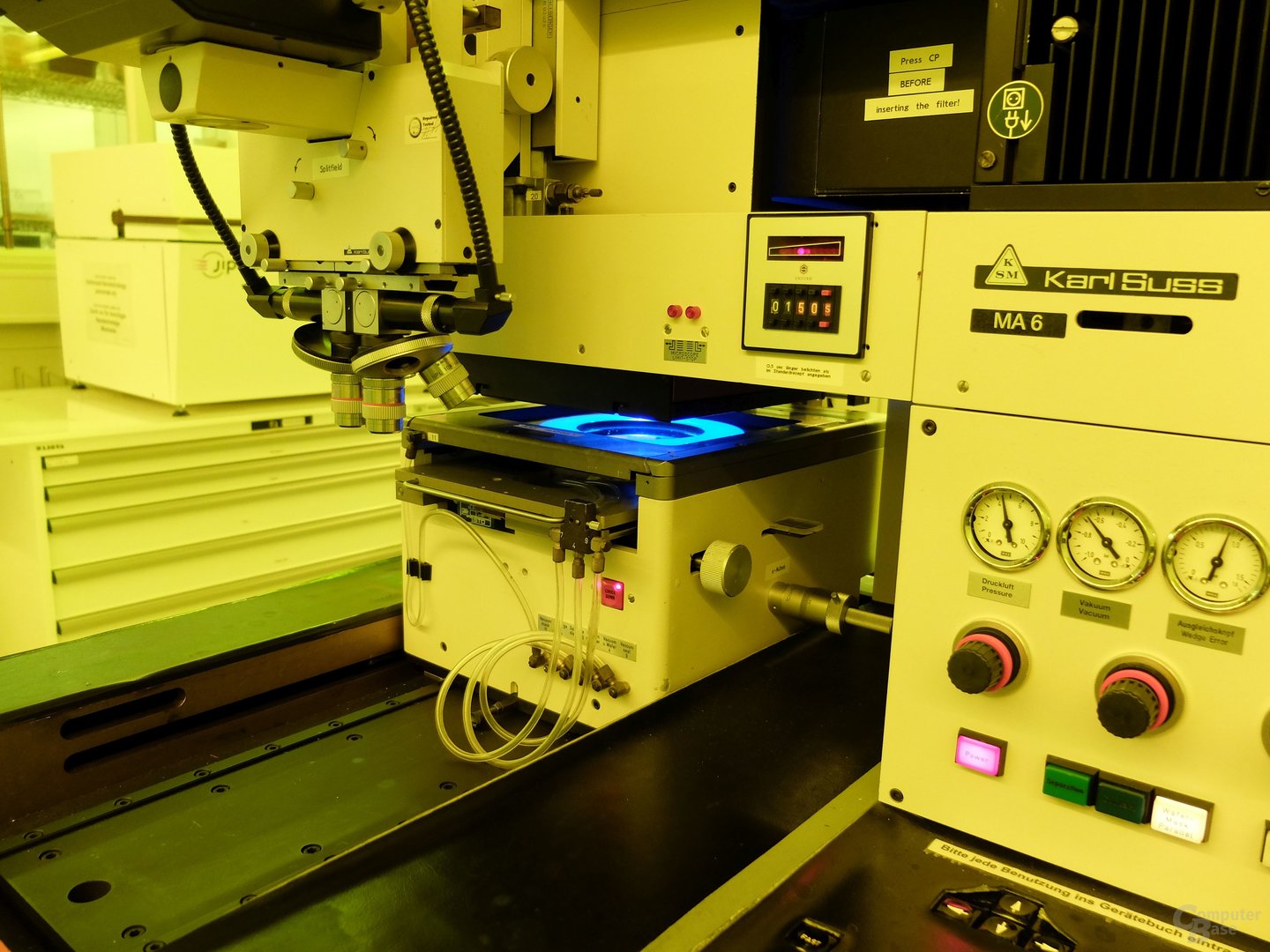