Nachhaltige Elektromobilität: Wie BMW in München die Akkus von morgen backt
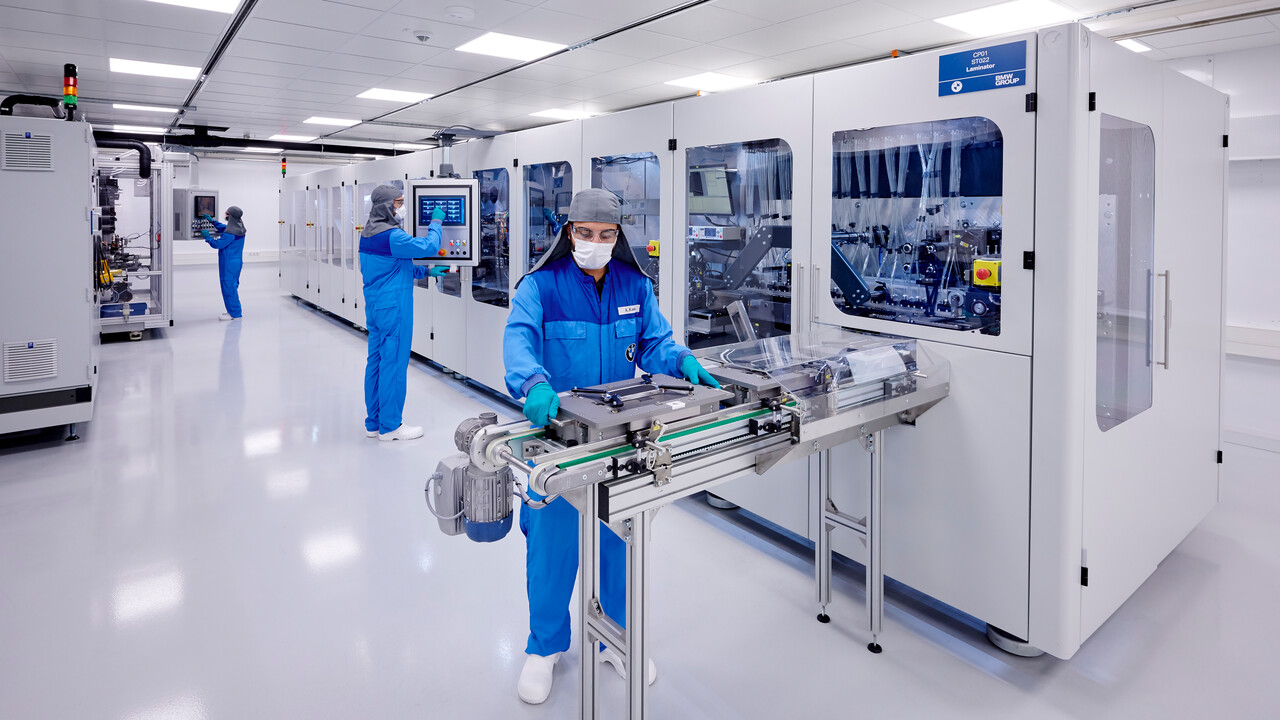
BMW hat sich zum Ziel gesetzt, bis 2030 die Energiedichte im Akku und die Reichweite von elektrifizierten Fahrzeugen zu verdoppeln. An den Batteriezellen der Zukunft forscht BMW in einem neuen Kompetenzzentrum in München. Die Produktion der Akkus übernehmen Partner, um die nachhaltige Rohstoffgewinnung will sich BMW kümmern.
Ein rein elektrisches Fahrzeug wie der BMW i3 (120 Ah) hat mit seinem 42,2-kWh-Akku eine praxisnahe Reichweite von 260 km. Das gesamte Akkusystem kommt auf ein Gewicht von 274 kg, sodass von einem Verhältnis von Gewicht des Akkus zu Reichweite von ungefähr eins zu eins gesprochen werden kann (1 km Reichweite je 1 kg Akkugewicht). BMW will die Energiedichte der Batteriezellen und damit auch die Reichweite von elektrifizierten Fahrzeugen bis 2030 verdoppeln, erklärte Oliver Zipse, Vorsitzender des Vorstands der BMW AG zur Eröffnung eines neuen Kompetenzzentrums für Batteriezellentechnologie in München.
Die Produktion bleibt bei Partnern
200 Millionen Euro für den Aufbau und 200 Mitarbeiter hat sich BMW das Kompetenzzentrum bisher kosten lassen. Der Standort verantwortet Forschung und Entwicklung, Zusammensetzung sowie das Design der Batteriezellen und soll die Produzierbarkeit in Großserie sicherstellen. Geforscht wird vor allem an neuen Materialsets für die Bestandteile einer Batteriezelle: Anode, Kathode, Elektrolyt und Separator. Der Konzern vergleicht die Entwicklung neuer Batteriezellen mit dem Kuchenbacken: Nur weil die gleichen Zutaten zum Einsatz kommen, schmecke nicht jeder Kuchen gleich gut. Am Münchener Standort entstehen sozusagen in einer experimentellen Konditorei eigene Backmischungen und Backverfahren für die Batteriezellen von morgen.
Die Produktion der Batteriezellen in Großserie wird BMW selbst allerdings nicht vornehmen. Hierbei vertraut das Unternehmen weiterhin auf die zwei wichtigsten Partner CATL (Contemporary Amperex Technology) aus China sowie Samsung SDI aus Südkorea. Erst bei der Fertigung des Batteriemoduls sowie der Endmontage zum Batteriepack, das in das Fahrzeug eingebaut wird, kommt BMW wieder ins Spiel. Nur die Blaupause zukünftiger Batteriezellen wird am neuen Standort München entwickelt und anschließend an die genannten Partner zur Produktion in Großserie weitergegeben.
Kobalt erst einmal nur noch aus Australien und Marokko
Wo die Rohstoffe der Batteriezellen herkommen und unter welchen Bedingungen diese gefördert werden, will BMW maßgeblich beeinflussen. Kobalt soll ab 2020 direkt bei Minen in Australien und Marokko eingekauft werden, anstatt diese über Zwischenhändler zu beziehen. Lithium soll unter anderem in Australien gefördert werden. Woher BMW seine Rohstoffe derzeit bezieht, lässt sich hier (PDF) einsehen. Bis 2025 und darüber hinaus würden die Lieferverträge eine Versorgungssicherheit garantieren, erklärte BMW. Da Kobalt in Australien und Marokko aber nur 7 Prozent der weltweiten Vorkommen abdecken und 58 Prozent im vielfach aufgrund der Abbaubedingungen kritisierten Kongo liegen, wird BMW zwangsweise dort aktiv werden müssen. In einem gemeinsamen Projekt mit BASF und Samsung SDI soll in einer kleinen Mine im Kongo der umweltgerechte und menschengerechte Abbau von Kobalt realisiert werden.
Recyclingquote von 90 Prozent als Ziel
Zur Nachhaltigkeit zählt aber auch das Recycling von Batteriezellen. Hier sieht BMW einen mehrstufigen Prozess für nicht mehr im Fahrzeug einsetzbare Batterien vor. Im ersten Schritt sollen diese als stationäre Speichersysteme zum Einsatz kommen, um die Netzstabilität zu erhöhen. Ist auch das nicht mehr möglich, soll das Recycling in einzelne Komponenten einsetzen, wobei die zur Entwicklung des i3 konzipierten Recycling-Techniken erst noch in den industriellen Maßstab überführt werden müssen. Auch daran und an verbesserten Recycling-Methoden wird im neuen Kompetenzzentrum geforscht. BMW hat sich eine Recyclingquote von 90 Prozent zum Ziel gesetzt – bisher jedoch ohne Stichtag für die Umsetzung.
Konkreter fallen die Absichten der Bayern bei der Elektrifizierung der Fahrzeugflotte aus. Zipse zufolge seien derzeit 7 Prozent der verkauften Fahrzeuge elektrifiziert, 2021 sollen es 25 Prozent sein, 2025 ein Drittel und 2030 die Hälfte aller ausgelieferten Fahrzeuge – dann ausgerüstet mit den neuen Batteriezellen mit doppelter Energiedichte und Reichweite. Um das zu erreichen, sollen ab 2023 25 elektrifizierte Autos angeboten werden. Dazu zählen vollelektrische Automobile und Plug-in-Hybride mit Verbrennungsmotor. Mehr als die Hälfte der 25 Modelle soll aber vollelektrisch sein. Mindestens 8 Jahre soll eine Batterie von BMW laut Zipse halten und niemals brennen.
Teslas Gigafactory 4 kommt nach Deutschland
Tesla, Anbieter rein elektrischer Fahrzeuge, hatte Anfang dieser Woche bekanntgegeben, ein Werk in Brandenburg nahe des Flughafen BER errichten zu wollen. In der „Gigafactory 4“ werden, dem Vorbild bestehender Tesla-Werke folgend, nicht nur Fahrzeuge (Model Y) montiert, sondern auch Komponenten wie die Batterie gefertigt. Die Batteriezellen fertigt aber auch Tesla nicht selbst, diese stammen von Panasonic und bald auch LG Chem. Zusammen mit dem für die Hauptstadt geplanten europäischen Design- und Entwicklungszentrum wird auch der E-Auto-Pionier in Zukunft also aktiv Forschung an der Batterie für Autos in Deutschland betreiben.
ComputerBase hat Informationen zu diesem Artikel von BMW auf einer Veranstaltung des Herstellers in München erhalten. Die Kosten für An- und Abreise wurden von BMW getragen. Eine Einflussnahme des Herstellers oder eine Verpflichtung zur Berichterstattung bestand nicht.