Vom Silizium zum Die: So werden aus Wafern im Reinraum Chips
2/2Belichtung macht noch keinen Die
Nach der Aktivierung der lichtsensitiven Komponente des Lacks auf dem Wafer sind zunächst noch keine augenscheinlichen Veränderungen auszumachen. Dafür muss die Siliziumscheibe in einen Entwickler, der durch ein speziell abgestimmtes Gemisch an Lösungsmitteln entweder die belichteten oder die unbelichteten Areale des Fotolacks vom Wafer wäscht – das hängt vom eingesetzten Fotolack ab. Der Entwickler nutzt dasselbe Prinzip wie beim Auftragen des Lacks: Auf einem Teller wird der Wafer per Vakuum angesaugt und rotiert, während in mehreren Schritten Flüssigkeiten des Entwicklers aufgesprüht werden.
Doch auch die nicht vom Entwickler entfernten Lackreste sind nicht irreversibel auf der Oberfläche des Wafers gebunden. Sie sind lediglich schwerer zu entfernen und dienen als Vorlage für die Übertragung der eigentlichen Strukturen, was über verschiedene Prozesse ablaufen kann. Sollen Vertiefungen im Wafer entstehen, so können Ätzprozesse wie zum Beispiel reaktives Ionenätzen („reactive ion etching“) oder nasschemisches gerichtetes Ätzen („wet etching“) mit Kaliumhydroxid genutzt werden. Die Ablagerung von Stoffen findet beispielsweise über chemische oder physikalische Gasphasenabscheidung statt (CVD und PVD).
Nach dem Entwicklungsvorgang werden Strukturen auf dem Wafer sichtbar: Die grün-rötlich schimmernden Bereiche des Wafers enthalten noch Lack, wohingegen dieser von der restlichen Fläche abgewaschen wurde. Die einzelnen Strukturen der Mikroheizelemente sind vielfach auf dem Wafer enthalten (ein Heizelement nimmt eine quadratische Fläche von 25 mm² ein), um möglichst viele Produkte je Wafer zu erhalten. Dadurch sinken die Kosten pro einzelnem Element. Im industriellen Maßstab werden daher größere Wafer mit einem Durchmesser von bis zu 30 cm eingesetzt.
Die einzelnen Produkte werden am Ende der Prozesskette über eine per Wasserstrahl gekühlte Säge als kleine Plättchen aus dem Wafer geschnitten und im Fachbegriff Die genannt. Doch bevor dies erfolgen kann, müssen zuerst noch mehrere Schichten Metall auf dem Wafer abgelagert werden, um die Heizelemente funktionsfähig zu machen. Im Moment liegt lediglich ein Silizium-Wafer mit strukturiertem Fotolack vor.
Physikalische Gasphasenabscheidung
Um die Mikroheizelemente tatsächlich auf den Wafer zu bekommen, werden die per Lack auf den Wafer übertragenen Strukturen in eine Metallbeschichtung verwandelt. Die Wafer erhalten über physikalische Gasphasenabscheidung zunächst 20 nm Chrom als Adhäsionsschicht und anschließend eine 100 nm dicke Nickelschicht als eigentliche Metallstruktur. Die Heizelemente selbst bestehen aus zwei (verhältnismäßig) großen Kontaktflächen, die über dünne, mäanderförmig verlaufende Metalllinien verbunden werden. Wenn am fertigen Endprodukt Spannung angelegt wird, heizen sich die dünnen Metalllinien durch den Stromfluss auf – fertig ist der Mikroheizer.
Die Elemente können alternativ auch als Temperatursensor fungieren, denn das Metall ändert in Abhängigkeit von der Temperatur seinen Widerstand. Durch die Messung des Widerstands kann bei Kenntnis der Schichtstruktur, der Länge der Metallbahnen auf dem Die sowie der Leitfähigkeit des Metalls selbst auf die aktuelle Temperatur zurückgeschlossen werden. Ein solcher temperaturabhängiger Widerstand wird als Thermistor bezeichnet.
Physikalische Gasphasenabscheidung bezeichnet einen Verdampfungsprozess, bei dem ein Metall bei sehr niedrigem Druck verdampft und auf einem Ziel abgelagert wird. In der Prozesskammer wird ein Druck von etwa 10^-7 mbar eingestellt und das zu verdampfende Metall mit einem gezielten Elektronenstrahl erhitzt. Der Elektronenstrahl sorgt für einen massiven lokalen Energieanstieg (die Schmelztiegel werden währenddessen wassergekühlt), wodurch das Metall verflüssigt wird, dann verdampft und sich in der Prozesskammer ausbreitet. Das Hochvakuum in der Kammer entspricht dem Druck im erdnahen Orbit im Weltall – als Vergleich: Auf Meereshöhe herrscht ein Druck von 1 bar. Dieses Hochvakuum ist unter anderem notwendig, um eine freie geradlinige Ausbreitung des Metalls in der Kammer zu ermöglichen, ohne dass es zur übermäßigen Ablenkung durch Gasmoleküle der Luft kommt.
Zwei verschiedene Pumpensysteme
Ein so niedriger Druck wird über zwei verschiedene Pumpen erzeugt. Zunächst wird Unterdruck durch eine „echte“ luftfördernde Drehschieberpumpe bis etwa 10^-2 mbar erzeugt. Als zweite Stufe steht eine Kryopumpe bereit, die eine Seite der Prozesskammer auf 10 bis 15 Kelvin (circa -260 °C) abkühlt und dort zur Kondensation der verbliebenen Luft in der Kammer führt. Die Gasmoleküle gehen in den flüssigen Aggregatzustand über und werden somit aus der Atmosphäre der Kammer entfernt – in der Folge sinkt der Druck. Der Arbeitsdruck in der PVD-Prozesskammer wird nach drei bis vier Stunden erreicht.
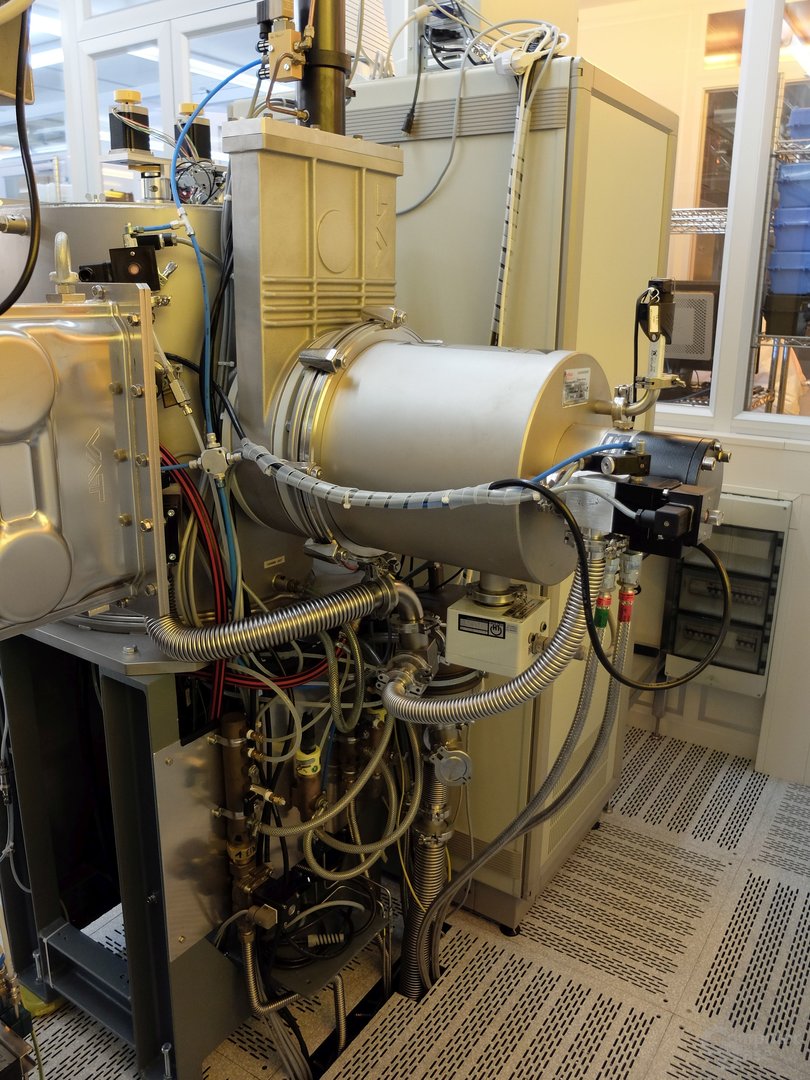
In der Kammer werden die Wafer mit der zu beschichtenden Seite nach unten auf einen drehenden Teller gelegt. Die Verdampfung der Metalle findet auf der unteren Seite der Kammer statt, so dass sich das verdampfte Metall nach oben bewegt und auf den Wafern als Metallschicht kondensiert. Zum Metall-Recycling wird die Prozesskammer mit Aluminiumfolie ausgekleidet: Da der Verdampfungsprozess in alle Richtungen abläuft, werden sämtliche Flächen innerhalb der Kammer gleichmäßig beschichtet. Mit dem Verfahren werden unter anderem Silber, Gold und Platin abgeschieden – teure Elemente, für die sich eine Wiedergewinnung lohnt. Die abgelagerten Metallschichten können nach mehreren Arbeitszyklen einfach entfernt und an spezialisierte Firmen verkauft werden, die die Metalle recyceln.
Die aktuelle Schichtdicke in der Prozesskammer wird über einen Quarzsensor ermittelt, auf dem ebenfalls Metall abgelagert wird. Der Sensor verändert seine Schwingfrequenz mit zunehmender Schichtdicke. Per Messung der aktuellen Schwingfrequenz erfolgt in Kombination mit der Kenntnis der Charakteristika des Metalls die genaue Berechnung der abgelagerten Schichtdicke. Die Abscheiderate der Anlage liegt (material- und leistungsabhängig) bei etwa 0,2 nm pro Sekunde.
Nach der Metallbeschichtung wird durch Aceton als Lösungsmittel und den unterstützenden Einsatz eines Ultraschallbads der verbliebene Fotolack auf dem Wafer entfernt (Lift-off-Verfahren). Da der gesamte Wafer mit Metall beschichtet wurde, kann das Lösungsmittel den Lack nicht mehr an den beschichteten Flächen, sondern nur an den vom Fotolack gebildeten „Seitenwänden“ angreifen, weshalb der Prozess durch Ultraschall beschleunigt wird. Am Ende trägt der Wafer nur noch an den Stellen eine Metallschicht, die vorher nicht von Fotolack bedeckt waren. Alle belackten Areale wurden zwar ebenfalls beschichtet, das Metall aber zusammen mit dem Lack entfernt. Damit ist die funktionale Nickel-Grundstruktur auf den Wafer übertragen – prinzipiell könnten die Heizelemente bereits arbeiten, doch für den tatsächlichen Einsatz werden noch weitere Arbeitsschritte benötigt.
Auf der Zielgeraden
Mit der Metallabscheidung ist der Besuch von ComputerBase im Reinraum beendet – die Bearbeitung der Wafer aber noch nicht. Für die restlichen Prozesse folgt daher lediglich eine kurze Zusammenfassung der einzelnen Schritte.
Insgesamt werden für die Mikroheizelemente drei Masken benutzt. Die Funktion der ersten Maske dient wie beschrieben der Übertragung der Struktur der Heizelemente auf die Wafer. Im Anschluss wird per chemischer Gasphasenabscheidung eine Schicht Siliziumnitrid auf die Wafer gebracht, um die empfindlichen dünnen und schmalen Metallstrukturen zu schützen.
Mit der zweiten Maske werden die Kontaktflächen für die Stromanschlüsse der Heizelemente wieder freigelegt. Per reaktivem Ionenätzen wird die Siliziumnitridschicht über den elektrischen Kontaktflächen abgetragen. Anschließend werden die Kontakte zur Verstärkung galvanisch mit Gold beschichtet.

Beim reaktiven Ionenätzen wird mittels eines speziellen Gasgemisches Plasma-getrieben die Siliziumnitrid-Passivierungsschicht vom Wafer entfernt. Die Beschichtung mit Gold findet in einer Lösung mit positiv geladenen Goldionen statt. Der Wafer dient als Kathode, weshalb sich das Gold an den freigesetzten Arealen ablagert. Die leitende Nickelschicht der Heizelemente bleibt also unter der schützenden Siliziumnitrid-Oberfläche verborgen, und nur die Kontaktflächen sind (verstärkt durch die Goldschicht) von außen zugänglich.
Belichtung von der gegenüberliegenden Seite
Für einen möglichst effizienten Einsatz der Heizelemente sollten die Metallbahnen, welche für die Erwärmung sorgen, so direkt wie möglich auf einer Zielstruktur aufliegen können. Daher wird die Rückseite des Wafers mit einer dritten Maske belichtet, die die Areale der Metallbahnen für einen Ätzvorgang durch den Siliziumwafer freilegt. Mit Kaliumhydroxid wird das Silizium der Wafer an diesen Stellen entfernt, bis noch etwa 70 µm Silizium unter den Metallstrukturen verbleiben. Im Vergleich zum dickeren Wafer überträgt diese dünne Membran die Wärme besser. Nun können die einzelnen Heizelemente aus dem Wafer geschnitten werden; pro 10-cm-Wafer entstehen so bis zu 156 Mikroheizelemente – sofern durch Verunreinigungen oder Fehler in der Prozesskette keine defekten Dies als Ausschuss enden.
Fazit
Dieser Artikel stellt natürlich kein umfassendes Werk zur Vielzahl an eingesetzten Prozessen der Mikrosystemtechnik und Mikroelektronik dar. Selbst die Beschreibungen der wenigen vorgestellten Arbeitsschritte kratzen lediglich an der Oberfläche der Theorie, die für ein fundiertes Verständnis vorausgesetzt wird.
Das ist allerdings auch nicht Sinn und Zweck dieses Berichts: Nicht umsonst beschäftigen sich Forscher seit Jahrzehnten an der Entwicklung immer ausgeklügelter Prozesse in der Halbleitertechnik, ohne die der heutige Alltag überhaupt nicht vorstellbar wäre.
Die Erfahrung beeindruckt noch mehr
Eine gewisse Entmystifizierung findet nach dem Besuch im Reinraum dennoch statt. Wenn man erst einmal selbst einen Wafer mit Fotolack beschichtet hat, so verliert der Begriff Lithographie seine abstrakte Natur – doch die Faszination und das Staunen darüber, was mittlerweile technisch machbar ist, wachsen umso mehr.
Das nachfolgende Video des Auftragsfertigers Globalfoundries gewährt einen weiteren Einblick in die Prozesse bei einem Chipfertiger, auch auf das Design der Mikrochips und die weiteren Verarbeitungsschritte wird in dem „Werbevideo“ eingegangen.
Dieser Artikel war interessant, hilfreich oder beides? Die Redaktion freut sich über jede Unterstützung durch ComputerBase Pro und deaktivierte Werbeblocker. Mehr zum Thema Anzeigen auf ComputerBase.